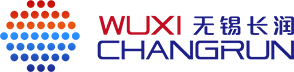
What Are You Looking For?
Heat exchanger is a device that transfers part of the heat of the hot fluid to the cold fluid. The heat exchanger is widely used in people's daily life and in industries such as petroleum, chemical industry, power, medicine, atomic energy and nuclear industry. It can be used as an independent device, such as a heater, condenser, cooler, etc.; It can also be used as a component of some process equipment, such as a heat exchanger in some chemical equipment.
Especially in the chemical industry with large energy consumption, heat exchangers are indispensable equipment in the process of heat exchange and transfer in chemical production, and they also occupy a considerable proportion of the entire chemical production equipment.
From the perspective of its function, the heat exchanger is on the one hand to ensure the specific temperature required for the medium by the industrial process, and on the other hand it is also the main equipment to improve energy utilization. According to its structural form, there are mainly plate heat exchangers, floating head heat exchangers, fixed tube plate heat exchangers, U-shaped tube heat exchangers, etc. Except for plate heat exchangers, the rest are shell and tube heat exchangers.
Because the shell and tube heat exchanger has a large heat exchange area per unit volume, good heat exchange effect, and has the advantages of solid structure, strong adaptability, and mature manufacturing technology, it has become the most commonly used typical heat exchanger.
Connection between heat exchange tubes and tube sheets in shell and tube heat exchangers
In a shell and tube heat exchanger, the heat exchange tube and tube plate are the only barriers between the tube side and the shell side of the heat exchanger. The connection structure and connection quality between the heat exchange tubes and the tube sheet determine the quality and service life of the heat exchanger. It is a crucial link in the heat exchanger manufacturing process.
Most damage and failure of heat exchangers occur at the connection between the heat exchange tube and the tube sheet. The quality of the connection joints directly affects the safety and reliability of chemical equipment and devices. Therefore, the connection process between the heat exchange tube and the tube plate in the shell and tube heat exchanger has become the most critical control link in the heat exchanger manufacturing quality assurance system. At present, in the manufacturing process of heat exchangers, the main methods for connecting heat exchange tubes and tube sheets include: welding, expanded, welded-and expanded, and bonding with expanded.
Welding
When the heat exchange tube is welded to the tube sheet, the process requirements for the tube sheet are low, the manufacturing process is simple, the sealing performance is good, and welding, visual inspection and maintenance are very convenient. It is one of the most widely used tube and tube plate connection methods in shell and tube heat exchangers. When welding is used for connection, there are strength welding that ensures the tightness and tensile strength of the welded joint and sealing welding that only ensures the tightness of the connection between the heat exchange tube and the tube plate. Strength welding has limited performance and is only suitable for situations with little vibration and no crevice corrosion.
When using different welding technologies to connect, the distance between the heat exchange tubes cannot be too close, otherwise the quality of the welds will not be fully guaranteed due to the influence of heat. At the same time, a certain distance should be left between the pipe ends to help reduce the mutual development of students. welding stress. The length of the heat exchange tube extending out of the tube plate must meet the requirements of relevant regulations to ensure its effective load-bearing management capability.
In terms of welding methods, depending on the materials of the heat exchanger tubes and tube plates, welding methods such as electrode arc welding, TIG welding, and CO2 welding can be used.
The traditional welding connection method is prone to gap corrosion and overheating due to the gap between the pipe and the tube plate hole. The thermal stress generated by the welded joint may also cause stress corrosion and damage, leading to heat exchanger failure.
At present, heat exchangers used in China's nuclear industry, power industry and other industries have adopted inner hole welding technology. This connection method changes the end welding of the heat exchange tube and the tube plate to the inner hole welding of the tube bundle. It adopts the full penetration form, which eliminates the gap in the end welding and improves the ability to resist gap corrosion and stress corrosion.
It has high vibration fatigue resistance, can withstand high temperature and high pressure, has good mechanical properties of welded joints, can control the internal quality of the weld, and improve the reliability of the weld.
However, the internal hole welding process is difficult to assemble, the welding process requirements are high, manufacturing and inspection are complex, and the manufacturing cost is relatively high. As heat exchangers develop towards high temperature, high pressure and large size, the requirements for their manufacturing quality are getting higher and higher, and inner hole welding technology will be more widely used.
Expanded tube-to-tubesheet joints
Expanded tube-to-tubesheet joints is a traditional Chinese method of connecting heat exchange tubes and tube sheets. Tube expansion equipment is used to produce elastic-plastic material deformation between the tube sheets and tubes to make them fit closer, forming a firmly established connection and achieving instant sealing. It has the purpose of resisting pull-off. In the manufacturing and development process of heat exchangers, expansion joints are suitable for situations where there is no severe vibration, no excessive temperature environment changes, and no severe stress to cause corrosion.
The currently used expansion processes mainly include mechanical rolling and hydraulic expansion.
Welded-And Expanded tube-to-tubesheet joints
When the temperature and pressure are high, and under the action of thermal deformation, thermal shock, thermal corrosion and fluid pressure, the connection between the heat exchange tube and the tube sheet is easily damaged, tt is difficult to ensure the connection strength and sealing requirements using expansion joints or welding.
At present, the method of combined expansion welding is widely used. The expansion joint and welding structure can effectively dampen the damage to the weld caused by the vibration of the tube bundle, effectively eliminate stress corrosion and gap corrosion, improve the fatigue resistance of the joint, thereby increasing the service life of the heat exchanger, which is better than simple expansion joint or Strength welding has higher strength and tightness. Ordinary heat exchangers usually use the form of "stick expansion% strength welding"; while heat exchangers with harsh operating conditions require the form of "strength expansion% sealing welding". According to the order of expansion and welding in the process, expansion jointing and welding can be divided into two types: expansion first and then welding, and welding first and then expansion.
(1) The lubricating oil that expands first and then welds penetrates into the joint gap and is very sensitive to welding cracks and pores, making welding defects more serious. The oil that has penetrated into the gap is difficult to clean, so do not use mechanical expansion during the welding process after the first expansion. Bonding expansion is not pressure-resistant, but it can eliminate the gap between the tube and the tube hole, thereby effectively damping the vibration of the tube bundle to the tube orifice welding part.
While conventional manual or mechanical expansion methods cannot meet the requirements for uniform expansion, the computer-controlled liquid bladder expansion method can meet the requirements for expansion conveniently and evenly. During the welding process, due to the influence of high-temperature molten metal, the gas in the gap is rapidly heated and expanded. When these high-temperature and high-pressure gases leak out, the sealing performance of the strength expansion will be damaged to a certain extent.
(2) Weld first and then expand. For the weld first and then expand process, the primary issue is the accuracy of the control system tubes and tube plate holes and their mutual cooperation. When the gap between the pipe and the tube plate hole is small enough to reach a certain value, the expansion process will not damage the quality of the welded joint. However, the ability of the max welding joint to withstand shear force is relatively poor. Therefore, when designing strength welding, if the control technology does not meet the standard requirements, it may cause over-expansion failure or expansion damage to the welded joint.
During the manufacturing process, there is a large gap between the outer diameter of the heat exchange tube and the tube hole of the tube sheet, and the gap between the outer diameter of each heat exchange tube and the tube hole of the tube sheet is uneven along the axial direction.
Bonding with expanded
The glue expansion joint process helps solve the leakage problem at the connection between the heat exchange tube and the tube plate of the heat exchanger. It is very important to correctly select the adhesive according to the working conditions of the adhesive joint. During the process implementation, process parameters should be selected according to the structure and size of the heat exchanger, mainly including curing pressure, curing temperature, expansion force, etc. , and strictly controlled during the production process. This process is simple, easy to implement, reliable, has been recognized in actual use by enterprises, and is worthy of promotion.
(1) In the connection method between the tubes and the tube sheets of the shell-and-tube heat exchanger, it is difficult to ensure the connection strength and sealing requirements by only using conventional welding or expansion joints.
(2) Research on the method of expansion joints and welding will help enterprises ensure the strength and sealing of the connection between the heat exchange tubes and the tube sheets, and improve the service life of my country's heat exchangers.
(3) The method of bonding and expansion joints can help solve leakage and leakage problems when connecting heat exchange tubes and tube sheets. The process is simple, feasible and reliable.
(4) The inner hole welding production technology can be used as a full penetration welding method to study. The ability to resist crevice corrosion and stress corrosion, the anti-vibration fatigue strength, and the mechanical model performance of the welded joint are all very good. The internal management quality analysis of welds can be effectively controlled, which improves the reliability of welds. First of all, it is more suitable for promotion, development and application in high-end enterprise products.